Standard Tools Not Cutting It? When To Go Custom
- CTIS
- Feb 7
- 3 min read
Updated: Feb 22
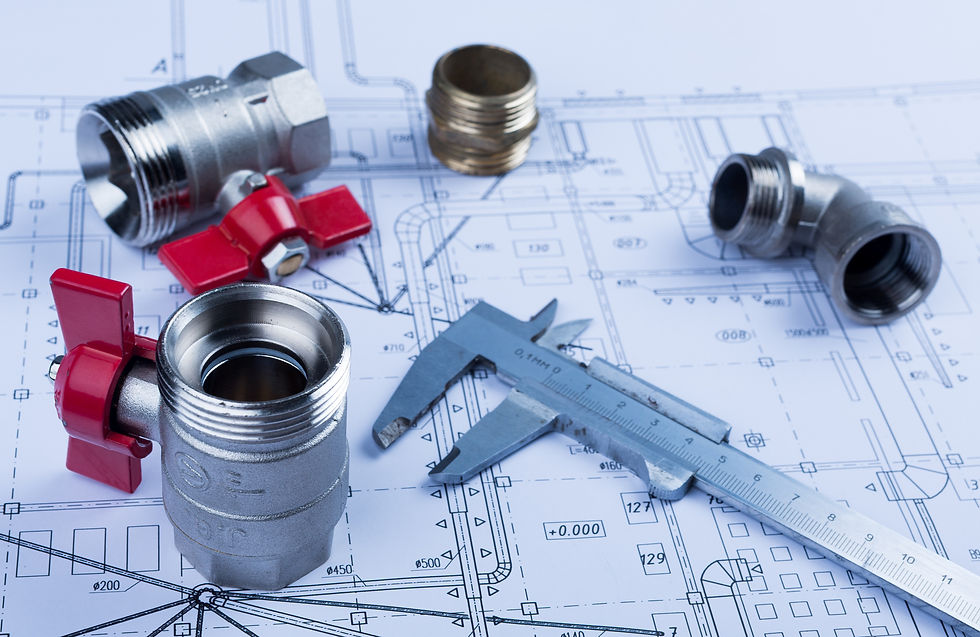
In the dynamic world of manufacturing, efficiency and precision are critical for staying competitive. Whether you are working in aerospace, automotive, medical device production, or another high-precision industry, the tools you use can significantly impact your production quality and output.
While standard tools are sufficient for many applications, there are situations where off-the-shelf solutions fall short. If your operations require highly specialized machining, extreme precision, or the ability to work with difficult materials, investing in custom tool design may be the key to optimizing your production process.
When to Consider Custom Tooling
Custom tool design becomes essential in scenarios where standard tools are unable to meet the specific demands of a project. Some common indicators that you may need a custom machining tool include:
1. Complex Geometries
Certain manufacturing applications require intricate part designs that standard tools cannot accurately produce. If your product requires unique cuts, angles, or shapes that are not achievable with mass-produced tooling, a custom solution ensures precision and repeatability.
2. Unique Materials
Some materials have specific properties that make them difficult to machine with traditional tools. Titanium, Inconel, hardened steel, and composite materials are commonly used in industries like aerospace and medical manufacturing. These materials require custom tools with specific geometries, coatings, and cutting edges to ensure clean cuts, reduce wear, and extend tool life.
3. Precision Requirements
Industries such as medical device manufacturing, semiconductor production, and aerospace engineering demand tight tolerances and high accuracy. If your components require exacting specifications, custom tooling can help eliminate deviations and ensure consistency across production runs.
4. High-Volume Production
For manufacturers producing large quantities of identical parts, custom tooling can streamline processes and reduce machining time. A tool designed for a specific application can perform multiple operations simultaneously, increasing efficiency and lowering per-unit costs.
Benefits of Custom Tool Design
Investing in custom machining tools comes with a range of advantages that go beyond precision and performance. Some key benefits include:
1. Enhanced Precision
Custom tools are specifically designed for the task at hand, ensuring higher accuracy in production. This minimizes defects, reduces rework, and improves the overall quality of the final product.
2. Increased Efficiency
A tool tailored to your exact application can reduce cycle times, improve workflow, and minimize tool changes. By eliminating inefficiencies caused by using multiple standard tools, a custom solution can streamline your manufacturing process.
3. Cost Savings Over Time
While custom tools often require a higher initial investment, the long-term cost savings can be significant. Improved tool longevity, reduced material waste, and faster production times all contribute to lower overall costs.
4. Extended Tool Life
Custom tools can be engineered with advanced coatings and materials to improve durability, especially when working with tough materials. This results in less frequent tool replacements and lower maintenance costs.
5. Competitive Advantage
Companies that utilize customized tooling solutions can produce higher-quality parts with greater efficiency. This leads to faster turnaround times, lower costs, and a stronger reputation in the market.
Partnering with CTIS for Custom Solutions
At CTIS, we understand that every manufacturing challenge is unique. That’s why we specialize in custom tool design and manufacturing, providing solutions tailored to your specific production requirements. Our process includes:
1. Consultation
Our experts take the time to understand your specific manufacturing challenges, production goals, and material requirements.
2. Design and Engineering
Using advanced CAD software and engineering expertise, we develop a custom tool optimized for your application. We factor in material composition, cutting geometry, and performance requirements.
3. Precision Manufacturing
Our state-of-the-art facilities use the latest CNC machining and tool fabrication technology to produce high-quality, durable custom tools.
4. Implementation and Support
We assist with integration into your production process, ensuring smooth operation and maximum performance. Our team also provides ongoing support for any modifications or enhancements.
Is Custom Tooling Right for You?
If you are encountering production inefficiencies, tool wear issues, or difficulties in machining certain materials, it may be time to consider a custom tool solution. Here are a few questions to ask when deciding:
Are standard tools failing to meet precision requirements?
Do you work with difficult-to-machine materials that cause excessive tool wear?
Would a custom tool reduce setup time, machining time, or material waste?
Are you looking for a solution that lowers long-term manufacturing costs?
If the answer is yes, custom tooling could be the game-changer your production process needs.

Contact CTIS Today
Ready to explore custom tooling solutions for your manufacturing needs? CTIS offers expertise in designing and implementing high-performance, precision-engineered tools that enhance productivity and efficiency. Contact us today!
Comments