Top 5 Signs Your Carbide Tools Need Reconditioning
- CTIS
- Feb 12
- 4 min read
Updated: Feb 22
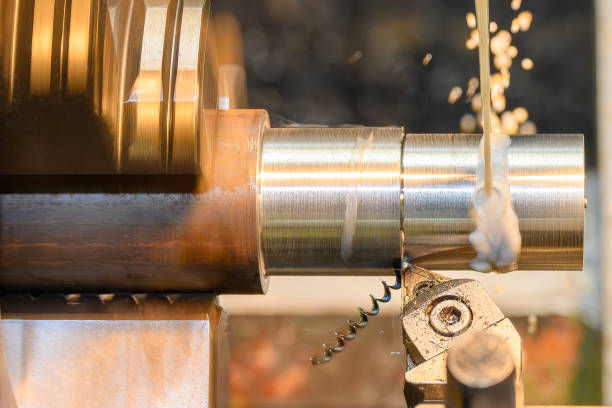
In the fast-paced world of manufacturing, your carbide tools are the backbone of efficiency and precision. Over time, even the most durable tools show signs of wear, and if left unaddressed, this can lead to decreased productivity and increased costs. Thankfully, reconditioning carbide tools is a cost-effective and sustainable way to extend their lifespan while maintaining top-notch performance.
In this guide, we’ll explore the key signs that your tools are ready for reconditioning, the benefits of addressing wear early, and how CTIS can help you maintain peak efficiency.
Why Carbide Tools Wear Out
Carbide tools are known for their durability, but no tool is invincible. With consistent use, factors such as heat, pressure, and friction take their toll. Some common causes of tool wear include:
High-speed machining: The faster the speed, the greater the heat generated, which impacts tool integrity.
Material hardness: Working with tough materials like stainless steel or hardened alloys increases wear rates.
Chip buildup: Poor chip evacuation can lead to tool edge damage.
The question isn’t if your carbide tools will wear out but when. That’s why it’s critical to recognize the signs and act quickly with reconditioning.
5 Signs Your Carbide Tools Need Reconditioning
1. Decline in Cutting Precision
If your cuts are no longer sharp and clean, and you’re noticing burrs or rougher edges, it’s a sure sign your tools are dulling. Reconditioning restores their sharpness and ensures your finished products maintain the high quality your customers expect.
2. Increased Vibration and Noise
Unusual vibrations or sounds during machining are often caused by uneven wear on cutting edges. These issues can compromise both your tool and your machinery if left unchecked. Reconditioning corrects the imbalance, preventing costly equipment damage.
3. Visible Wear on Cutting Edges
Inspect your tools regularly. Chips, cracks, or dull edges mean your tools are past their prime. Reconditioning doesn’t just fix these visible flaws—it brings tools back to their original performance levels.
4. Reduced Production Speeds
Are tasks taking longer than they used to? Worn tools lose efficiency, slowing down production lines and causing delays. Reconditioning ensures your tools operate at peak speed without compromising accuracy.
5. Higher Power Consumption
When tools dull, they require more power to achieve the same results. This not only drives up energy costs but also increases the environmental impact of your operations. Reconditioning restores sharpness, reducing the power needed and saving you money.
The Cost-Saving Benefits of Reconditioning
Reconditioning is a fraction of the cost of replacing your tools outright. Here’s how it benefits your bottom line:
Extended tool lifespan: A single tool can be reconditioned multiple times, maximizing its value.
Reduced downtime: Reconditioned tools perform like new, keeping your operations running smoothly.
Improved sustainability: Fewer tools discarded means less waste, aligning your business with eco-friendly practices.
Think of reconditioning as an investment—not just in your tools, but in the overall efficiency and cost-effectiveness of your business.
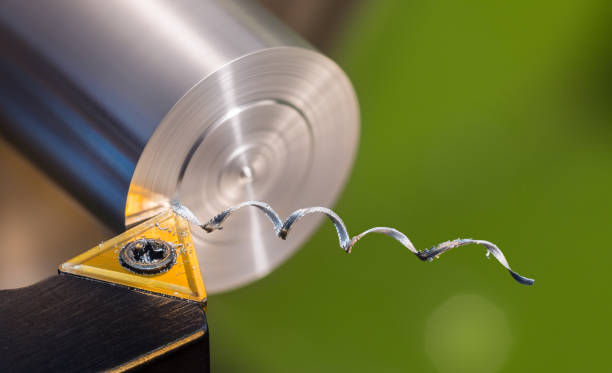
How the Reconditioning Process Works at CTIS
At CTIS, we don’t just restore your tools; we optimize them for peak performance. Here’s what our process looks like:
Inspection:
Every tool undergoes a thorough examination to determine its condition and whether reconditioning is viable. If a tool is beyond repair, we’ll recommend replacement.
Precision Grinding:
Using advanced grinding equipment, we restore the cutting edges to their original geometry. This step ensures tools regain their sharpness and precision.
Advanced Coating Application:
For enhanced performance, we apply high-quality coatings like titanium nitride (TiN) or titanium aluminum nitride (TiAlN). These coatings reduce friction, resist heat, and extend tool life.
Final Quality Check:
Each reconditioned tool is inspected rigorously to ensure it meets industry standards and your specific requirements.
This meticulous process ensures that reconditioned tools perform as effectively as new ones, delivering value without compromise.
Common Questions About Reconditioning
Q: How many times can a carbide tool be reconditioned?
A: Most tools can be reconditioned 3–5 times, depending on their original quality and the extent of wear. Our experts at CTIS will assess each tool to determine its reconditioning potential.
Q: Is reconditioning as effective as buying new tools?
A: Yes! Properly reconditioned tools can match the performance of new tools, especially when handled by a professional team like CTIS.
Q: How do I know when it’s time to recondition?
A: Regularly inspect your tools for signs of wear, such as dull edges, slower performance, or unusual vibrations. If you’re unsure, CTIS can provide a detailed evaluation.
Real-World Success: Reconditioning in Action
One of our clients in the oil and gas industry faced frequent tool replacements due to wear from machining hardened alloys. By implementing a regular reconditioning program with CTIS, they:
Cut tool replacement costs by 40%.
Reduced downtime by 25%.
Achieved consistent product quality across all production runs.
This success story highlights how reconditioning isn’t just a repair—it’s a strategy for long-term efficiency and cost savings.
Partner with CTIS for Expert Reconditioning
When it comes to reconditioning, experience and precision matter. At CTIS, we bring decades of expertise and cutting-edge technology to every tool we restore. Here’s why clients trust us:
Customized Solutions: We tailor our services to meet your specific industry and tooling requirements.
Fast Turnaround: Minimize downtime with our efficient reconditioning process.
Eco-Friendly Practices: Support sustainable manufacturing with reduced tooling waste.

Extend the Life of Your Tools Today
Reconditioning carbide tools is more than just a cost-saving measure—it’s a smart, sustainable approach to maintaining operational efficiency. By addressing wear early and partnering with CTIS, you can ensure your tools perform at their best while reducing waste and downtime.
Ready to recondition your tools? Contact CTIS today to schedule a consultation and experience the benefits of professional tool restoration.
Comments